Kamis, 24 November 2011
Relay dan Kontaktor (Relay and Magnetic Contactor)
Relay dan Kontaktor (Relay and Magnetic Contactor)
Pemahaman sederhananya adalah bila kita memberikan arus listrik pada coil relay atau kontaktor, maka saklar internalnya juga akan terhubung. Selain itu juga ada saklar internalnya yang terputus. Hal tersebut sama persis pada kerja tombol push button, hanya berbeda pada kekuatan untuk menekan tombolnya.
Saklar internal inilah yang disebut sebagai kontak NO (Normally Open= Bila coil contactor atau relay dalam keadaan tak terhubung arus listrik, kontak internalnya dalam kondisi terbuka atau tak terhubung) dan kontak NC (Normally Close= Sebaliknya dengan Normally Open). Seperti dijelaskan pada gambar dibawah ini.
Relay dianalogikan sebagai pemutus dan penghubung seperti halnya fungsi pada tombol (Push Button) dan saklar (Switch)., yang hanya bekerja pada arus kecil 1A s/d 5A. Sedangkan Kontaktor dapat di analogikan juga sebagai sebagai Breaker untuk sirkuit pemutus dan penghubung tenaga listrik pada beban. Karena pada Kontaktor, selain terdapat kontak NO dan NC juga terdapat 3 buah kontak NO utama yang dapat menghubungkan arus listrik sesuai ukuran yang telah ditetapkan pada kontaktor tersebut. Misalnya 10A, 15A, 20A, 30A, 50Amper dan seterusnya. Seperti pada gambar dibawah ini.
gambar kontak internal pada Kontaktor
Penyambungan sederhana rangkaian kontaktor:
Perhatikan bagaimana lampu akan menyala ketika switch saklar dihubungkan ke sumber listrik. Mengapa begitu repot menggunakan kontaktor untuk menyalakan sebuah lampu bohlam? Mengapa rangkain ini menggunakan dua buah sumber listrik yang berbeda?
Itulah yang disebut Rangkain Pengendali dan Rangkain Utama.
Time Delay Relay (Timer) dan Thermal Over Load Relay (Tripper)


Kegunaan NO dan NC
Setelah paham bagaimana kerja kontak NO dan NC yang terdapat pada peralatan tersebut diatas, maka saya sarankan untuk mempelajari bagaimana kontak NO NC tersebut digunakan semaksimal mungkin untuk sebuah rangkaian pengendali pada rangkaian utama.
Setelah paham bagaimana kerja kontak NO dan NC yang terdapat pada peralatan tersebut diatas, maka saya sarankan untuk mempelajari bagaimana kontak NO NC tersebut digunakan semaksimal mungkin untuk sebuah rangkaian pengendali pada rangkaian utama.
Time Delay Relay
TDR (Time Delay Relay) sering disebut juga relay timer atau relay penunda batas waktu banyak digunakan dalam instalasi motor terutama instalasi yang membutuhkan pengaturan waktu secara otomatis.
Peralatan kontrol ini dapat dikombinasikan dengan peralatan kontrol lain, contohnya dengan MC (Magnetic Contactor), Thermal Over Load Relay, dan lain-lain.
Fungsi
dari peralatan kontrol ini adalah sebagai pengatur waktu bagi
peralatan yang dikendalikannya. Timer ini dimaksudkan untuk mengatur
waktu hidup atau mati dari kontaktor atau untuk merubah sistem bintang
ke segitiga dalam delay waktu tertentu.
Timer dapat dibedakan dari cara kerjanya yaitu timer yang bekerja menggunakan induksi motor dan menggunakan rangkaian elektronik.
Timer yang bekerja dengan prinsip induksi motor akan bekerja bila motor
mendapat tegangan AC sehingga memutar gigi mekanis dan memarik serta
menutup kontak secara mekanis dalam jangka waktu tertentu.
Sedangkan
relay yang menggunakan prinsip elektronik, terdiri dari rangkaian R
dan C yang dihubungkan seri atau paralel. Bila tegangan sinyal telah
mengisi penuh kapasitor, maka relay akan terhubung. Lamanya waktu tunda
diatur berdasarkan besarnya pengisisan kapasitor.
Bagian input timer biasanya dinyatakan sebagai kumparan (Coil) dan bagian outputnya sebagai kontak NO atau NC.
Kumparan
pada timer akan bekerja selama mendapat sumber arus. Apabila telah
mencapai batas waktu yang diinginkan maka secara otomatis timer akan
mengunci dan membuat kontak NO menjadi NC dan NC menjadi NO.
Pada umumnya timer memiliki 8 buah kaki yang 2 diantaranya merupakan kaki coil sebagai contoh pada gambar di atas adalah TDR type H3BA dengan 8 kaki yaitu kaki 2 dan 7 adalah kaki coil,
sedangkan kaki yang lain akan berpasangan NO dan NC, kaki 1 akan NC
dengan kaki 4 dan NO dengan kaki 3. Sedangkan kaki 8 akan NC dengan
kaki 5 dan NO dengan kaki 6. Kaki kaki tersebut akan berbeda tergantung
dari jenis relay timernya.
Minggu, 13 November 2011
PLC (PROGRAMMABLE LOGIC CONTROLLER)
2.1 Pengertian
Programmable
Logic Controllers (PLC) adalah komputer elektronik yang mudah digunakan (user
friendly) yang memiliki fungsi kendali untuk berbagai tipe dan tingkat
kesulitan yang beraneka ragam [2].
Definisi
Programmable Logic Controller menurut Capiel (1982) adalah :
sistem elektronik yang beroperasi secara
dijital dan didisain untuk pemakaian di lingkungan industri, dimana sistem ini
menggunakan memori yang dapat diprogram untuk penyimpanan secara internal
instruksi-instruksi yang mengimplementasikan fungsi-fungsi spesifik seperti
logika, urutan, perwaktuan, pencacahan dan operasi aritmatik untuk mengontrol
mesin atau proses melalui modul-modul I/O dijital maupun analog [3].
Berdasarkan namanya konsep PLC
adalah sebagai berikut :
1.
Programmable
menunjukkan
kemampuan dalam hal memori untuk menyimpan program yang telah dibuat yang
dengan mudah diubah-ubah fungsi atau kegunaannya.
2.
Logic
menunjukkan
kemampuan dalam memproses input secara aritmatik dan logic (ALU), yakni
melakukan operasi membandingkan, menjumlahkan, mengalikan, membagi, mengurangi,
negasi, AND, OR, dan lain sebagainya.
3.
Controller
menunjukkan
kemampuan dalam mengontrol dan mengatur proses sehingga menghasilkan output
yang diinginkan.
PLC ini dirancang untuk menggantikan suatu rangkaian relay
sequensial dalam suatu sistem kontrol. Selain dapat
diprogram, alat ini juga dapat dikendalikan, dan dioperasikan oleh orang yang
tidak memiliki pengetahuan di bidang pengoperasian komputer secara khusus. PLC
ini memiliki bahasa pemrograman yang mudah dipahami dan dapat
dioperasikan bila program yang telah dibuat dengan menggunakan software yang
sesuai dengan jenis PLC yang digunakan sudah dimasukkan.
Alat ini bekerja berdasarkan input-input yang ada dan
tergantung dari keadaan pada suatu waktu tertentu yang kemudian akan meng-ON
atau meng-OFF kan output-output. 1 menunjukkan bahwa keadaan yang diharapkan terpenuhi sedangkan 0 berarti
keadaan yang diharapkan tidak terpenuhi. PLC juga dapat diterapkan untuk
pengendalian sistem yang memiliki output banyak.
Fungsi dan kegunaan PLC sangat
luas. Dalam prakteknya PLC dapat dibagi secara umum dan secara khusus [4].
Secara umum fungsi PLC adalah sebagai berikut:
1.
Sekuensial
Control
PLC
memproses input sinyal biner menjadi output yang digunakan untuk keperluan
pemrosesan teknik secara berurutan (sekuensial), disini PLC menjaga agar
semua step atau langkah dalam proses sekuensial berlangsung dalam urutan yang
tepat.
2.
Monitoring
Plant
PLC secara
terus menerus memonitor status suatu sistem (misalnya temperatur, tekanan,
tingkat ketinggian) dan mengambil tindakan yang diperlukan sehubungan dengan
proses yang dikontrol (misalnya nilai sudah melebihi batas) atau menampilkan
pesan tersebut pada operator.
Sedangkan
fungsi PLC secara khusus adalah dapat memberikan input ke CNC (Computerized
Numerical Control). Beberapa PLC dapat memberikan input ke CNC untuk
kepentingan pemrosesan lebih lanjut. CNC bila dibandingkan dengan PLC mempunyai
ketelitian yang lebih tinggi dan lebih mahal harganya. CNC biasanya dipakai
untuk proses finishing, membentuk benda kerja, moulding dan sebagainya.
Prinsip
kerja sebuah PLC adalah menerima sinyal masukan proses yang dikendalikan lalu
melakukan serangkaian instruksi logika terhadap sinyal masukan tersebut sesuai
dengan program yang tersimpan dalam memori lalu menghasilkan sinyal keluaran
untuk mengendalikan aktuator atau peralatan lainnya.
![]() |
Gambar 2.1 Hubungan PLC dengan CNC
2.2
Keuntungan dan Kerugian PLC [2][5]
Dalam industri-industri yang ada
sekarang ini, kehadiran PLC sangat dibutuhkan terutama untuk menggantikan
sistem wiring atau pengkabelan yang sebelumnya masih digunakan dalam
mengendalikan suatu sistem. Dengan menggunakan PLC akan diperoleh banyak
keuntungan diantaranya adalah sebagai berikut:
Ø
Fleksibel
Pada masa lalu, tiap perangkat
elektronik yang berbeda dikendalikan dengan pengendalinya masing-masing. Misal
sepuluh mesin membutuhkan sepuluh pengendali, tetapi kini hanya dengan satu PLC
kesepuluh mesin tersebut dapat
dijalankan dengan programnya masing-masing.
Ø
Perubahan dan pengkoreksian kesalahan sistem lebih mudah
Bila salah satu sistem akan diubah atau
dikoreksi maka pengubahannya hanya dilakukan pada program yang terdapat di
komputer, dalam waktu yang relatif singkat, setelah itu didownload ke PLC-nya.
Apabila tidak menggunakan PLC, misalnya relay maka perubahannya dilakukan
dengan cara mengubah pengkabelannya. Cara ini tentunya memakan waktu yang lama.
Ø
Jumlah kontak yang banyak
Jumlah kontak yang dimiliki oleh PLC
pada masing-masing coil lebih banyak daripada kontak yang dimiliki oleh sebuah
relay.
Ø
Harganya lebih murah
PLC mampu menyederhanakan banyak
pengkabelan dibandingkan dengan sebuah relay. Maka harga dari sebuah PLC lebih
murah dibandingkan dengan harga beberapa buah relay yang mampu melakukan
pengkabelan dengan jumlah yang sama dengan sebuah PLC. PLC mencakup relay,
timers, counters, sequencers, dan berbagai fungsi lainnya.
Ø Pilot running
PLC yang terprogram dapat dijalankan dan
dievaluasi terlebih dahulu di kantor atau laboratorium. Programnya dapat
ditulis, diuji, diobserbvasi dan dimodifikasi bila memang dibutuhkan dan hal
ini menghemat waktu bila dibandingkan dengan sistem relay konvensional yang
diuji dengan hasil terbaik di pabrik.
Ø
Observasi visual
Selama program dijalankan, operasi pada
PLC dapat dilihat pada layar CRT. Kesalahan dari operasinya pun dapat diamati
bila terjadi.
Ø
Kecepatan operasi
Kecepatan operasi PLC lebih cepat
dibandingkan dengan relay. Kecepatan PLC ditentukan dengan waktu scannya dalam
satuan millisecond.
Ø
Metode Pemrograman Ladder atau Boolean
Pemrograman PLC dapat dinyatakan dengan
pemrograman ladder bagi teknisi, atau aljabar Boolean bagi programmer yang
bekerja di sistem kontrol digital atau Boolean.
Ø
Sifatnya tahan uji
Solid state device lebih tahan uji
dibandingkan dengan relay dan timers mekanik atau elektrik. PLC merupakan solid
state device sehingga bersifat lebih tahan uji.
Ø
Menyederhanakan komponen-komponen sistem kontrol
Dalam PLC juga terdapat counter, relay
dan komponen-komponen lainnya, sehingga tidak membutuhkan komponen-komponen
tersebut sebagai tambahan. Penggunaan relay membutuhkan counter, timer ataupun
komponen-komponen lainnya sebagai peralatan tambahan.
Ø
Dokumentasi
Printout dari PLC dapat langsung diperoleh
dan tidak perlu melihat blueprint circuit-nya.
Tidak seperti relay yang printout sirkuitnya tidak dapat diperoleh.
Ø
Keamanan
Pengubahan pada PLC tidak dapat
dilakukan kecuali PLC tidak dikunci dan diprogram. Jadi tidak ada orang yang
tidak berkepentingan dapat mengubah program PLC selama PLC tersebut dikunci.
Ø
Dapat melakukan pengubahan dengan pemrograman ulang
Karena PLC dapat diprogram ulang secara
cepat, proses produksi yang bercampur dapat diselesaikan. Misal bagian B akan
dijalankan tetapi bagian A masih dalam proses, maka proses pada bagian B dapat
diprogram ulang dalam satuan detik.
Ø Penambahan rangkaian lebih cepat
Pengguna dapat menambah rangkaian
pengendali sewaktu-waktu dengan cepat, tanpa memerlukan tenaga dan biaya yang
besar seperti pada pengendali konvensional.
Selain keuntungan yang telah disebutkan di atas maka ada
kerugian yang dimiliki oleh PLC, yaitu:
Ø
Teknologi yang masih baru
Pengubahan sistem kontrol lama yang
menggunakan ladder atau relay ke konsep komputer PLC merupakan hal yang sulit
bagi sebagian orang
Ø
Buruk untuk aplikasi program yang tetap
Beberapa aplikasi merupakan aplikasi
dengan satu fungsi. Sedangkan PLC dapat mencakup beberapa fungsi sekaligus.
Pada aplikasi dengan satu fungsi jarang sekali dilakukan perubahan bahkan tidak
sama sekali, sehingga penggunaan PLC pada aplikasi dengan satu fungsi akan
memboroskan (biaya).
Ø
Pertimbangan lingkungan
Dalam suatu pemrosesan, lingkungan
mungkin mengalami pemanasan yang tinggi, vibrasi yang kontak langsung dengan
alat-alat elektronik di dalam PLC dan hal ini bila terjadi terus menerus,
mengganggu kinerja PLC sehingga tidak berfungsi optimal.
Ø
Operasi dengan rangkaian yang tetap
Jika rangkaian pada sebuah operasi tidak
diubah maka penggunaan PLC lebih mahal dibanding dengan peralatan kontrol
lainnya. PLC akan menjadi lebih efektif bila program pada proses tersebut di-upgrade secara periodik.
2.3 Rangkaian Start-Stop [5]
Banyak sistem mempunyai sebuah
sistem Master Control Relay untuk Safety Shutdown pada operasi
PLC. Ketika ON, safety shutdown mengijinkan PLC untuk beroperasi. Ketika
di-deenergize, maka PLC tidak akan beroperasi. Tipe sistem master
shutdown seperti yang terlihat pada
gambar di halaman berikut:

Gambar 2.2 Skema Master Control Safety Shutdown
Pada gambar di atas jika tombol
Start di tekan (ON) maka coil MCR akan ter-energize sehingga anak relay MCR
akan ter-energize pula sehingga PLC akan beroperasi. Walaupun tombol Start
kembali ke posisinya semula (OFF), coil MCR tetap ter-energize karena adanya
anak relay MCR lain pararel dengan tombol Start. Ketika tombol Stop ditekan
(OFF), maka rangkaian menjadi terbuka yang menyebabkan tidak ada lagi aliran
arus ke coil MCR, sehingga coil MCR tidak ter-energize lagi. Karena coil MCR
tidak ter-energize lagi maka dua anak relaynya akan OFF sehingga PLC akan OFF
(tidak beroperasi).
Pada gambar di atas terdapat pula Emergency
Stop Pushbutton yang digunakan apabila terjadi sesuatu pada sistem sehingga
sistem harus dimatikan. Selain itu terdapat sebuah limit switch yang
berhubungan dengan pintu dimana sistem PLC diletakkan. Apabila pintu tersebut
dibuka maka limit switch OFF sehingga coil MCR tidak ter-energize yang
menyebabkan sistem PLC akan OFF, apabila pintu ditutup maka limit switch akan
ON sehingga sistem PLC akan ON pula. Sedangkan Suppressor digunakan
untuk mengurangi atau menghilangkan
sinyal gangguan dari luar yang dapat membuat program sistem PLC menjadi malfunction.
2.4 Bagian-Bagian PLC
Sistem PLC terdiri dari lima
bagian pokok, yaitu:
Ø Central
processing unit (CPU).
Bagian ini
merupakan otak atau jantung PLC, karena bagian ini merupakan bagian yang
melakukan operasi / pemrosesan program yang tersimpan dalam PLC. Disamping itu
CPU juga melakukan pengawasan atas semua operasional kerja PLC, transfer
informasi melalui internal bus antara PLC, memory dan unit I/O.
Bagian CPU ini antara lain
adalah :
q Power Supply, power supply mengubah suplai masukan listrik
menjadi suplai listrik yang sesuai dengan CPU dan seluruh komputer.
q Alterable Memory, terdiri dari banyak bagian, intinya bagian ini
berupa chip yang isinya di letakkan pada chip RAM (Random Access Memory),
tetapi isinya dapat diubah dan dihapus oleh pengguna / pemrogram. Bila
tidak ada supplai listrik ke CPU maka isinya akan hilang, oleh sebab itu bagian ini disebut bersifat volatile, tetapi ada juga bagian yang tidak bersifat volatile.
q Fixed Memory, berisi program yang sudah diset oleh pembuat PLC,
dibuat dalam bentuk chip khusus yang dinamakan ROM (Read Only Memory),
dan tidak dapat diubah atau dihapus selama operasi CPU, karena itu bagian ini
sering dinamakan memori non-volatile yang tidak akan terhapus isinya
walaupun tidak ada listrik yang masuk ke dalam CPU. Selain itu dapat juga
ditambahkan modul EEPROM atau Electrically Erasable Programmable Read Only Memory yang ditujukan untuk back up program
utama RAM prosesor sehingga prosesor dapat diprogram untuk meload program
EEPROM ke RAM jika program di RAM hilang atau rusak [6].
q Processor, adalah bagian yang mengontrol supaya informasi tetap jalan dari bagian yang satu ke bagian
yang lain, bagian ini berisi rangkaian clock, sehingga masing-masing
transfer informasi ke tempat lain tepat sampai pada waktunya
q Battery Backup, umumnya CPU memiliki bagian ini. Bagian ini
berfungsi menjaga agar tidak ada kehilangan program yang telah dimasukkan ke
dalam RAM PLC jika catu daya ke PLC tiba-tiba terputus.
Ø Programmer
/ monitor (PM).
Pemrograman
dilakukan melalui keyboard sehingga alat ini dinamakan Programmer. Dengan
adanya Monitor maka dapat dilihat apa yang diketik atau proses yang
sedang dijalankan oleh PLC. Bentuk PM ini ada yang besar seperti PC, ada juga
yang berukuran kecil yaitu hand-eld programmer dengan jendela tampilan yang
kecil, dan ada juga yang berbentuk laptop. PM dihubungkan dengan CPU melalui
kabel. Setelah CPU selesai diprogram maka PM tidak dipergunakan lagi untuk
operasi proses PLC, sehingga bagian ini hanya dibutuhkan satu buah untuk banyak
CPU.

Fiber optics
cables
Or
Twisted pair of wires plus ground
Or
Coaxial
Cable Multiple
wires To input
Multiple wires
optional To output
remote
connection up to One Mile
I/O module
optional connection
to
Connections
master
computer
to
input
switches
contacts, etc
Connections
To
Outputs-
Coils
Alarms,etc
Gambar 2.3 Layout Sistem PLC dan koneksinya
Ø Modul
input / output (I/O).
Input merupakan bagian yang menerima sinyal
elektrik dari sensor atau komponen lain dan sinyal itu dialirkan ke PLC untuk
diproses. Ada banyak jenis modul input yang dapat dipilih dan jenisnya
tergantung dari input yang akan digunakan. Jika input adalah limit
switches dan pushbutton dapat dipilih kartu input DC. Modul input
analog adalah kartu input khusus yang menggunakan ADC (Analog to Digital Conversion) dimana kartu ini digunakan untuk input
yang berupa variable seperti temperatur, kecepatan, tekanan dan posisi.
Pada umumnya ada 8-32 input point setiap modul inputnya. Setiap
point akan ditandai sebagai alamat yang unik oleh prosesor.
Output adalah bagian PLC yang menyalurkan sinyal
elektrik hasil pemrosesan PLC ke peralatan output. Besaran informasi / sinyal
elektrik itu dinyatakan dengan tegangan listrik antara 5 - 15 volt DC dengan
informasi diluar sistem tegangan yang bervariasi antara 24 - 240 volt DC mapun
AC. Kartu output biasanya mempunyai 6-32 output point dalam
sebuah single module. Kartu output analog adalah tipe khusus dari modul output
yang menggunakan DAC (Digital to Analog Conversion). Modul output analog dapat mengambil nilai dalam 12 bit dan
mengubahnya ke dalam signal analog. Biasanya signal ini 0-10 volts DC atau 4-20
mA. Signal Analog biasanya digunakan pada peralatan seperti motor yang
mengoperasikan katup dan pneumatic position control devices.
Bila
dibutuhkan, suatu sistem elektronik dapat ditambahkan untuk menghubungkan modul
ini ke tempat yang jauh. Proses operasi sebenarnya di bawah kendali PLC mungkin
saja jaraknya jauh, dapat saja ribuan meter.
Ø Printer.
Alat ini
memungkinkan program pada CPU dapat di printout atau dicetak. Informasi yang
mungkin dicetak adalah diagram ladder, status register, status dan daftar dari
kondisi-kondisi yang sedang dijalankan, timing diagram dari kontak, timing
diagram dari register, dan lain-lain.
Ø The
Program Recorder / Player.
Alat ini digunakan
untuk menyimpan program dalam CPU. Pada PLC yang lama digunakan tape, sistem floopy
disk. Sekarang ini PLC semakin berkembang
dengan adanya hard disk yang digunakan untuk pemrograman dan perekaman. Program
yang telah direkam ini nantinya akan direkam kembali ke dalam CPU apabila
program aslinya hilang atau mengalami kesalahan.
Untuk
operasi yang besar, kemungkinan lain adalah menghubungkan CPU dengan komputer
utama (master computer) yang biasanya
digunakan pada pabrik besar atau proses yang mengkoodinasi banyak Sistem PLC .
2.5 Konsep Perancangan Sistem Kendali dengan PLC [7][8]
Dalam merancang suatu sistem kendali
dibutuhkan pendekatan-pendekatan sistematis dengan prosedure sebagai berikut :
1. Rancangan Sistem Kendali
Dalam tahapan
ini si perancang harus menentukan terlebih dahulu sistem apa yang akan
dikendalikan dan proses bagaimana yang akan ditempuh. Sistem yang dikendalikan
dapat berupa peralatan mesin ataupun proses yang terintegrasi yang sering
secara umum disebut dengan controlled system.
2. Penentuan I/O
Pada tahap ini semua piranti masukan dan
keluaran eksternal yang akan dihubungkan PLC harus ditentukan. Piranti masukan
dapat berupa saklar, sensor, valve dan lain-lain sedangkan piranti keluaran
dapat berupa solenoid katup elektromagnetik dan lain-lain.
3. Perancangan Program (Program Design)
Setelah ditentukan input dan output maka
dilanjutkan dengan proses merancang
program dalam bentuk ladder diagram dengan mengikuti aturan dan urutan operasi
sistem kendali.
4. Pemrograman (Programming)
5. Menjalankan Sistem (Run The System)
Pada tahapan ini perlu dideteksi adanya
kesalahan-kesalahan satu persatu (debug), dan menguji secara cermat sampai kita
memastikan bahwa sistem aman untuk dijalankan.
Kamis, 10 November 2011
Dasar-Dasar Pneumatik

Pneumatik menggunakan hukum-hukum aeromekanika, yang menentukan keadaan keseimbangan gas dan uap (khususnya udara atmosfir) dengan adanya gaya-gaya luar (aerostatika) dan teori aliran (aerodinamika). Pneumatik dalam pelaksanaan teknik udara mampat dalam industri merupakan ilmu pengetahuan dari semua proses mekanik dimana udara memindahkan suatu gaya atau gerakan. Jadi pneumatik meliputi semua komponen mesin atau peralatan, dalam mana terjadi proses-proses pneumatik. Dalam bidang kejuruan teknik pneumatik dalam pengertian yang lebih sempit lagi adalah teknik udara mampat (udara bertekanan).
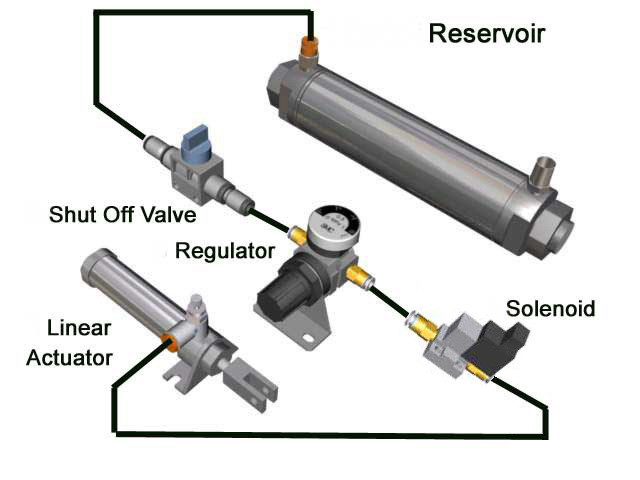

Komponen-komponen Pneumatik
Komponen pneumatik beroperasi pada tekanan 8 s.d. 10 bar, tetapi dalam praktik dianjurkan beroperasi pada tekanan 5 s.d. 6 bar untuk penggunaan yang ekonomis.
Beberapa bidang aplikasi di industri yang menggunakan media pneumatik dalam hal penangan material adalah sebagai berikut :
a. Pencekaman benda kerja
b. Penggeseran benda kerja
c. Pengaturan posisi benda kerja
d. Pengaturan arah benda kerja
Penerapan pneumatik secara umum :
a. Pengemasan (packaging)
b. Pemakanan (feeding)
c. Pengukuran (metering)
d. Pengaturan buka dan tutup (door or chute control)
e. Pemindahan material (transfer of materials)
f. Pemutaran dan pembalikan benda kerja (turning and inverting of parts)
g. Pemilahan bahan (sorting of parts)
h. Penyusunan benda kerja (stacking of components)
i. Pencetakan benda kerja (stamping and embosing of components)
Susunan sistem pneumatik adalah sebagai berikut :
a. Catu daya (energi supply)
b. Elemen masukan (sensors)
c. Elemen pengolah (processors)
d. Elemen kerja (actuators)
1.1 Alasan Pemakaian Pneumatik
Persaingan antara peralatan pneumatik dengan peralatan mekanik, hidrolik atau elektrik makin menjadi besar. Dalam penggunaannya sistem pneumatik diutamakan karena beberapa hal yaitu :
a. paling banyak dipertimbangkan untuk beberapa mekanisasi,
b. dapat bertahan lebih baik terhadap keadaan-keadaan tertentu
Sering kali suatu proses tertentu dengan cara pneumatik, berjalan lebih rapi (efisien) dibandingkan dengan cara lainnya. Contoh :
1). Palu-palu bor dan keling pneumatik adalah jauh lebih baik dibandingkan dengan perkakas-perkakas elektrik serupa karena lebih ringan, lebih ada kepastian kerja dan lebih sederhana dalam pelayanan.
2). Pesawat-pesawat pneumatik telah mengambil suatu kedudukan monopoli yang penting pada :
a). rem-rem udara bertekanan untuk mobil angkutan dan gerbong-gerbong kereta api, alat-alat angkat dan alat-alat angkut.
b). pistol-pistol ( alat cat semprot, mesin-mesin peniup kaca, berbagai jenis penyejukan udara, kepala-kepala asah kecepatan tinggi ).
Udara bertekanan memiliki banyak sekali keuntungan, tetapi dengan sendirinya juga terdapat segi-segi yang merugikan atau lebih baik pembatasan-pembatasan pada penggunaannya. Hal-hal yang menguntungkan dari pneumatik pada mekanisasi yang sesuai dengan tujuan sudah diakui oleh cabang-cabang industri yang lebih banyak lagi. Pneumatik mulai digunakan untuk pengendalian maupun penggerakan mesin-mesin dan alat-alat.
1.2 Keuntungan Pemakaian Pneumatik
a. Merupakan media/fluida kerja yang mudah didapat dan mudah diangkut :
1). Udara dimana saja tersedia dalam jumlah yang tak terhingga.
2). Saluran-saluran balik tidak diperlukan karena udara bekas dapat dibuang bebas ke atmosfir, sistem elektrik dan hidrolik memerlukan saluran balik.
3). Udara bertekanan dapat diangkut dengan mudah melalui saluran-saluran dengan jarak yang besar, jadi pembuangan udara bertekanan dapat dipusatkan dan menggunakan saluran melingkar semua pemakai dalam satu perusahaan dapat dilayani udara bertekanan dengan tekanan tetap dan sama besarnya. Melalui saluran-saluran cabang dan pipa-pipa selang, energi udara bertekanan dapat disediakan dimana saja dalam perusahaan.
b. Dapat disimpan dengan mudah :
1). Sumber udara bertekanan ( kompresor ) hanya menyerahkan udara bertekanan kalau udara bertekanan ini memang digunakan. Jadi kompresor tidak perlu bekerja seperti halnya pada pompa peralatan hidrolik.
2). Pengangkutan ke dan penyimpanan dalam tangki-tangki penampung juga dimungkinkan.
3). Suatu daur kerja yang telah dimulai selalu dapat diselesaikan, demikian pula kalau penyediaan listrik tiba-tiba dihentikan.
c. Bersih dan kering :
1). Udara bertekanan adalah bersih. Kalau ada kebocoran pada saluran pipa, benda-benda kerja maupun bahan-bahan disekelilingnya tidak akan menjadi kotor.
2). Udara bertekanan adalah kering. Bila terdapat kerusakan pipa-pipa tidak akan ada pengotoran-pengotoran, bintik minyak dansebagainya.
3). Dalam industri pangan , kayu , kulit dan tenun serta pada mesin-mesin pengepakan hal yang memang penting sekali adalah bahwa peralatan tetap bersih selama bekerja.
Sistem pneumatik yang bocor bekerja merugikan dilihat dari sudut ekonomis, tetapi dalam keadaan darurat pekerjaan tetap dapat berlangsung. Tidak terdapat minyak bocoran yang mengganggu seperti pada sistem hidrolik.
d. Tidak peka terhadap suhu
1). Udara bersih ( tanpa uap air ) dapat digunakan sepenuhnya pada suhu-suhu yang tinggi atau pada nilai-nilai yang rendah, jauh di bawah titik beku ( masing-masing panas atau dingin ).
2). Udara bertekanan juga dapat digunakan pada tempat-tempat yang sangat panas, misalnya untuk pelayanan tempa tekan, pintu-pintu dapur pijar, dapur pengerasan atau dapur lumer.
3). Peralatan-peralatan atau saluran-saluran pipa dapat digunakan secara aman dalam lingkungan yang panas sekali, misalnya pada industri-industri baja atau bengkel-bengkel tuang (cor).
e. Aman terhadap kebakaran dan ledakan
1). Keamanan kerja serta produksi besar dari udara bertekanan tidak mengandung bahaya kebakaran maupun ledakan.
2). Dalam ruang-ruang dengan resiko timbulnya kebakaran atau ledakan atau gas-gas yang dapat meledak dapat dibebaskan, alat-alat pneumatik dapat digunakan tanpa dibutuhkan pengamanan yang mahal dan luas. Dalam ruang seperti itu kendali elektrik dalam banyak hal tidak diinginkan.
f. Tidak diperlukan pendinginan fluida kerja
1). Pembawa energi (udara bertekanan) tidak perlu diganti sehingga untuk ini tidak dibutuhkan biaya. Minyak setidak-tidaknya harus diganti setelah 100 sampai 125 jam kerja.
g. Rasional (menguntungkan)
1). Pneumatik adalah 40 sampai 50 kali lebih murah daripada tenaga otot. Hal ini sangat penting pada mekanisasi dan otomatisasi produksi.
2). Komponen-komponen untuk peralatan pneumatik tanpa pengecualian adalah lebih murah jika dibandingkan dengan komponen-komponen peralatan hidrolik.
h. Kesederhanaan (mudah pemeliharaan)
1). Karena konstruksi sederhana, peralatan-peralatan udara bertekanan hampir tidak peka gangguan.
2). Gerakan-gerakan lurus dilaksanakan secara sederhana tanpa komponen mekanik, seperti tuas-tuas, eksentrik, cakera bubungan, pegas, poros sekerup dan roda gigi.
3). Konstruksinya yang sederhana menyebabkan waktu montase (pemasangan) menjadi singkat, kerusakan-kerusakan seringkali dapat direparasi sendiri, yaitu oleh ahli teknik, montir atau operator setempat.
4). Komponen-komponennya dengan mudah dapat dipasang dan setelah dibuka dapat digunakan kembali untuk penggunaan-penggunaan lainnya.
i. Sifat dapat bergerak
1). Selang-selang elastik memberi kebebasan pindah yang besar sekali dari komponen pneumatik ini.
j. Aman
1). Sama sekali tidak ada bahaya dalam hubungan penggunaan pneumatik, juga tidak jika digunakan dalam ruang-ruang lembab atau di udara luar. Pada alat-alat elektrik ada bahaya hubungan singkat.
k. Dapat dibebani lebih ( tahan pembebanan lebih )
Alat-alat udara bertekanan dan komponen-komponen berfungsi dapat ditahan sedemikian rupa hingga berhenti. Dengan cara ini komponen-komponen akan aman terhadap pembebanan lebih. Komponen-komponen ini juga dapat direm sampai keadaan berhenti tanpa kerugian.
1). Pada pembebanan lebih alat-alat udara bertekanan memang akan berhenti, tetapi tidak akan mengalami kerusakan. Alat-alat listrik terbakar pada pembebanan lebih.
2). Suatu jaringan udara bertekanan dapat diberi beban lebih tanpa rusak.
3). Silinder-silinder gaya tak peka pembebanan lebih dan dengan menggunakan katup-katup khusus maka kecepatan torak dapat disetel tanpa bertingkat.
l. Jaminan bekerja besar
Jaminan bekerja besar dapat diperoleh karena :
1). Peralatan serta komponen bangunannya sangat tahan aus.
2). Peralatan serta komponen pada suhu yang relatif tinggi dapat digunakan sepenuhnya dan tetap demikian.
3). Peralatan pada timbulnya naik turun suhu yang singkat tetap dapat berfungsi.
4). Kebocoran-kebocoran yang mungkin ada tidak mempengaruhi ketentuan bekerjanya suatu instalasi.
m. Biaya pemasangan murah
1). Mengembalikan udara bertekanan yang telah digunakan ke sumbernya (kompresor) tidak perlu dilakukan. Udara bekas dengan segera mengalir keluar ke atmosfir, sehingga tidak diperlukan saluran-saluran balik, hanya saluran masuk saja.
2). Suatu peralatan udara bertekanan dengan kapasitas yang tepat, dapat melayani semua pemakai dalam satu industri. Sebaliknya, pengendalian-pengendalian hidrolik memerlukan sumber energi untuk setiap instalasi tersendiri (motor dan pompa).
n. Pengawasan (kontrol)
1). Pengawasan tekanan kerja dan gaya-gaya atas komponen udara bertekanan yang berfungsi dengan mudah dapat dilaksanakan dengan pengukur-pengukur tekanan (manometer).
o. Fluida kerja cepat
1). Kecepatan-kecepatan udara yang sangat tinggi menjamin bekerjanya elemen-elemen pneumatik dengan cepat. Oleh sebab itu waktu menghidupkan adalah singkat dan perubahan energi menjadi kerja berjalan cepat.
2). Dengan udara mampat orang dapat melaksanakan jumlah perputaran yang tinggi ( Motor Udara ) dan kecepatan-kecepatan piston besar (silinder-silinder kerja ).
3). Udara bertekanan dapat mencapai kecepatan alir sampai 1000 m/min (dibandingkan dengan energi hidrolik sampai 180 m/min ).
4). Dalam silinder pneumatik kecepatan silinder dari 1 sampai 2 m/detik mungkin saja ( dalam pelaksanaan khusus malah sampai 15 m/detik ).
5). Kecepatan sinyal-sinyal kendali pada umumnya terletak antara 40 dan 70 m/detik (2400 sampai 4200 m/min)
p. Dapat diatur tanpa bertingkat
1). Dengan katup pengatur aliran, kecepatan dan gaya dapat diatur tanpa bertingkat mulai dari suatu nilai minimum (ditentukan oleh besarnya silinder) sampai maksimum (tergantung katup pengatur yang digunakan).
2). Tekanan udara dengan sederhana dan kalau dibutuhkan dalam keadaan sedang bekerja dapat disesuaikan dengan keadaan.
3). Beda perkakas rentang tenaga jepitnya dapat disetel dengan memvariasikan tekanan udara tanpa bertingkat dari 0 sampai 6 bar.
4). Tumpuan-tumpuan dapat disetel guna mengatur panjang langkah silinder kerja yang dapat disetel terus-menerus (panjang langkah ini dapat bervariasi sembarang antara kedua kedudukan akhirnya).
5). Perkakas-perkakas pneumatik yang berputar dapat diatur jumlah putaran dan momen putarnya tanpa bertingkat.
q. Ringan sekali
Berat alat-alat pneumatik jauh lebih kecil daripada mesin yang digerakkan elektrik dan perkakas-perkakas konstruksi elektrik (hal ini sangat penting pada perkakas tangan atau perkakas tumbuk). Perbandingan berat (dengan daya yang sama) antara :
• motor pneumatik : motor elektrik = 1 : 8 (sampai 10)
• motor pneumatik : motor frekuensi tinggi = 1 : 3 (sampai 4)
r. Kemungkinan penggunaan lagi (ulang)
Komponen-komponen pneumatik dapat digunakan lagi, misalnya kalau komponen-komponen ini tidak dibutuhkan lagi dalam mesin tua.
r. Konstruksi kokoh
Pada umumnya komponen pneumatik ini dikonstruksikan secara kompak dan kokoh, dan oleh karena itu hampir tidak peka terhadap gangguan dan tahan terhadap perlakuan-perlakuan kasar.
s. Fluida kerja murah
Pengangkut energi (udara) adalah gratis dan dapat diperoleh senantiasa dan dimana saja. Yang harus dipilih adalah suatu kompresor yang tepat untuk keperluan tertentu; jika seandainya kompresor yang dipilih tidak memenuhi syarat, maka segala keuntungan pneumatik tidak ada lagi.
1.3 Kerugian / terbatasnya Pneumatik
a. Ketermampatan (udara).
Udara dapat dimampatkan. Oleh sebab itu adalah tidak mungkin untuk mewujudkan kecepatan-kecepatan piston dan pengisian yang perlahan-lahan dan tetap, tergantung dari bebannya.
Pemecahan :
• kesulitan ini seringkali diberikan dengan mengikutsertakan elemen hidrolik dalam hubungan bersangkutan, tertama pada pengerjaan-pengerjaan cermat ( bor, bubut atau frais ) hal ini merupakan suatu alat bantu yang seringkali digunakan.
b. Gangguan Suara (Bising)
Udara yang ditiup ke luar menyebabkan kebisingan (desisan) mengalir ke luar, terutama dalam ruang-ruang kerja sangat mengganggu.
Pemecahan :
• dengan memberi peredam suara (silincer)
c. Kegerbakan (volatile)
Udara bertekanan sangat gerbak (volatile). Terutama dalam jaringan-jaringan udara bertekanan yang besar dan luas dapat terjadi kebocoran-kebocoran yang banyak, sehingga udara bertekanan mengalir keluar. Oleh karena itu pemakaian udara bertekanan dapat meningkat secara luar biasa dan karenanya harga pokok energi “berguna” sangat tinggi.
Pemecahan :
• dapat dilakukan dengan menggunakan perapat-perapat berkualitas tinggi.
d. Kelembaban udara
Kelembaban udara dalam udara bertekanan pada waktu suhu menurun dan tekanan meningkat dipisahkan sebagai tetesan air (air embun).
Pemecahan :
• penggunaan filter-filter untuk pemisahan air embun (dan juga untuk penyaring kotoran-kotoran).
e. Bahaya pembekuan
Pada waktu pemuaian tiba-tiba (dibelakang pemakai udara bertekanan) dan penurunan suhu yang bertalian dengan pemuaian tiba-tiba ini, dapat terjadi pembentukan es.
Pemecahan :
• Batasi pemuaian udara bertekanan dalam perkakas-perkakas pneumatik.
• Biarkan udara memuai sepenuhnya pada saat diadakan peniupan ke luar.
f. Kehilangan energi dalam bentuk kalor.
Energi kompresi adiabatik dibuang dalam bentuk kalor dalam pendingin antara dan akhir. Kalor ini hilang sama sekali dan kerugian ini hampir tidak dapat dikurangi.
g. Pelumasan udara bertekanan
Oleh karena tidak adanya sistem pelumasan untuk bagian-bagian yang bergerak, maka bahan pelumas ini dimasukkan bersamaan dengan udara yang mengalir, untuk itu bahan pelumas harus dikabutkan dalam udara bertekanan.
h. Gaya tekan terbatas
1). Dengan udara bertekanan hanya dapat dibangkitkan gaya yang terbatas saja. Untuk gaya yang besar, pada tekanan jaringan normal dibutuhkan diameter piston yang besar.
2). Penyerapan energi pada tekanan-tekanan kejutan hidrolik dapat memberi jalan keluar.
i. Ketidakteraturan
Suatu gerakan teratur hampir tidak dapat diwujudkan :
1). Pada pembebanan berganti-ganti
2). Pada kecepatan-kecepatan kecil (kurang dari 0,25 cm/det) dapat timbul ‘stick-slip effect’.
j. Tidak ada sinkronisasi
Menjalankan dua silinder atau lebih paralel sangat sulit dilakukan.
k. Biaya energi tinggi
Biaya produksi udara bertekanan adalah tinggi. Oleh karena itu untuk produksi dan distribusi dibutuhkan peralatan-peralatan khusus. Setidak-tidaknya biaya ini lebih tinggi dibandingkan dengan penggerak elektrik.
Perbandingan biaya ( tergantung dari cara penggerak ) :
• Elektrik : Pneumatik = 1 : 10 (sampai 12)
• Elektrik : Hidrolik = 1 : 8 (sampai 10)
• Elektrik : Tangan = 1 : 400 (sampai 500)
1.4 Pemecahan Kerugian Pneumatik
Pada umumnya, hal-hal yang merugikan dapat dikurangi atau dikompensasi dengan :
a. Peragaman yang cocok dari komponen-komponen maupun alat pneumatik.
b. Pemilihan sebaik mungkin sistem pneumatik yang dibutuhkan.
c. Kombinasi yang sesuai dengan tujuannya dari berbagai sistem penggerakan dan pengendalian (elektrik, pneumatik dan hidrolik).
kontaktor
KONTAKTOR
Kontaktor adalah jenis saklar yang bekerja secara magnetik yaitu
kontak bekerja apabila kumparan diberi energi. The National Manufacture
Assosiation (NEMA) mendefinisikan kontaktor magnetis sebagai alat yang
digerakan secara magnetis untuk menyambung dan membuka rangkaian daya
listrik. Tidak seperti relay, kontaktor dirancang untuk menyambung dan
membuka rangkaian daya listrik tanpa merusak. Beban-beban tersebut
meliputi lampu, pemanas, transformator, kapasitor, dan motor listrik.
Prinsip Kerja
Sebuah kontaktor terdiri dari koil, beberapa kontak Normally Open ( NO ) dan beberapa Normally Close ( NC ). Pada saat satu kontaktor normal, NO akan membuka dan pada saat kontaktor bekerja, NO akan menutup. Sedangkan kontak NC sebaliknya yaitu ketika dalam keadaan normal kontak NC akan menutup dan dalam keadaan bekerja kontak NC akan membuka. Koil adalah lilitan yang apabila diberi tegangan akan terjadi magnetisasi dan menarik kontak-kontaknya sehingga terjadi perubahan atau bekerja. Kontaktor yang dioperasikan secara elektromagnetis adalah salah satu mekanisme yang paling bermanfaat yang pernah dirancang untuk penutupan dan pembukaan rangkaian listrik maka gambar prinsip kerja kontaktor magnet dapat dilihat pada gambar berikut :
Karakteristik
Spesifikasi kontaktor magnet yang harus diperhatikan adalah kemampuan daya kontaktor ditulis dalam ukuran Watt / KW, yang disesuaikan dengan beban yang dipikul, kemampuan menghantarkan arus dari kontak – kontaknya, ditulis dalam satuan ampere, kemampuan tegangan dari kumparan magnet, apakah untuk tegangan 127 Volt atau 220 Volt, begitupun frekuensinya, kemampuan melindungi terhadap tegangan rendah, misalnya ditulis ± 20 % dari tegangan kerja. Dengan demikian dari segi keamanan dan kepraktisan, penggunaan kontaktor magnet jauh lebih baik dari pada saklar biasa.
Aplikasi
Keuntungan penggunaan kontaktor magnetis sebagai pengganti peralatan kontrol yang dioperasikan secara manual meliputi hal :
a.Pada penangan arus besar atau tegangan tinggi, sulit untuk membangun alat manual yang cocok. Lebih dari itu, alat seperti itu besar dan sulit mengoperasikannya. Sebaliknya, akan relatif sederhana untuk membangun kontaktor magnetis yang akan menangani arus yang besar atau tegangan yang tinggi, dan alat manual harus mengontrol hanya kumparan dari kontaktor.
b.Kontaktor memungkinkan operasi majemuk dilaksanakan dari satu operator (satu lokasi) dan diinterlocked untuk mencegah kesalahan dan bahaya operasi.
c.Pengoperasian yang harus diulang beberapa kali dalam satu jam, dapat digunakan kontaktor untuk menghemat usaha. Operator secara sederhana harus menekan tombol dan kontaktor akan memulai urutan event yang benar secara otomatis.
d.Kontaktor dapat dikontrol secara otomatis dengan alat pilot atau sensor yang sangat peka.
e.Tegangan yang tinggi dapat diatasi oleh kontaktor dan menjauhkan seluruhnya dari operator, sehingga meningkatkan keselamatan / keamanan instalasi.
f.Dengan menggunakan kontaktor peralatan kontrol dapat dipasangkan pada titik-titik yang jauh. Satu-satunya ruang yang diperlukan dekat mesin adalah ruangan untuk tombol tekan.
g.Dengan kontaktor, kontrol otomatis dan semi otomatis mungkin dilakukan dengan peralatan seperti kontrol logika yang dapat diprogram seperti Programmable Logic Controller (PLC).
PLC
2.1 Pengertian
Programmable
Logic Controllers (PLC) adalah komputer elektronik yang mudah digunakan (user
friendly) yang memiliki fungsi kendali untuk berbagai tipe dan tingkat
kesulitan yang beraneka ragam [2].
Definisi Programmable Logic Controller menurut Capiel (1982)
adalah :
sistem elektronik yang
beroperasi secara dijital dan didisain untuk pemakaian di lingkungan industri,
dimana sistem ini menggunakan memori yang dapat diprogram untuk penyimpanan
secara internal instruksi-instruksi yang mengimplementasikan fungsi-fungsi
spesifik seperti logika, urutan, perwaktuan, pencacahan dan operasi aritmatik
untuk mengontrol mesin atau proses melalui modul-modul I/O dijital maupun
analog [3].
Berdasarkan namanya
konsep PLC adalah sebagai berikut :
1. Programmable
menunjukkan kemampuan
dalam hal memori untuk menyimpan program yang telah dibuat yang dengan mudah
diubah-ubah fungsi atau kegunaannya.
2. Logic
menunjukkan kemampuan
dalam memproses input secara aritmatik dan logic (ALU), yakni melakukan operasi
membandingkan, menjumlahkan, mengalikan, membagi, mengurangi, negasi, AND, OR,
dan lain sebagainya.
3. Controller
menunjukkan kemampuan
dalam mengontrol dan mengatur proses sehingga menghasilkan output yang diinginkan.
PLC ini dirancang untuk menggantikan suatu
rangkaian relay sequensial dalam suatu sistem kontrol. Selain dapat diprogram, alat ini
juga dapat dikendalikan, dan dioperasikan oleh orang yang tidak memiliki
pengetahuan di bidang pengoperasian komputer secara khusus. PLC ini memiliki
bahasa pemrograman yang mudah dipahami dan dapat
dioperasikan bila program yang telah dibuat dengan menggunakan software yang
sesuai dengan jenis PLC yang digunakan sudah dimasukkan.
Alat ini bekerja berdasarkan input-input yang
ada dan tergantung dari keadaan pada suatu waktu tertentu yang kemudian akan
meng-ON atau meng-OFF kan output-output. 1 menunjukkan bahwa
keadaan yang diharapkan terpenuhi sedangkan 0 berarti keadaan yang diharapkan
tidak terpenuhi. PLC juga dapat diterapkan untuk pengendalian sistem yang
memiliki output banyak.
Fungsi dan kegunaan PLC
sangat luas. Dalam prakteknya PLC dapat dibagi secara umum dan secara khusus
[4].
Secara umum fungsi PLC adalah sebagai
berikut:
. Sekuensial
Control
PLC memproses input
sinyal biner menjadi output yang digunakan untuk keperluan pemrosesan teknik
secara berurutan (sekuensial), disini PLC menjaga agar semua step atau
langkah dalam proses sekuensial berlangsung dalam urutan yang tepat.
2. Monitoring
Plant
PLC secara terus menerus
memonitor status suatu sistem (misalnya temperatur, tekanan, tingkat
ketinggian) dan mengambil tindakan yang diperlukan sehubungan dengan proses
yang dikontrol (misalnya nilai sudah melebihi batas) atau menampilkan pesan
tersebut pada operator.
Sedangkan fungsi PLC secara khusus adalah dapat memberikan input ke CNC (Computerized
Numerical Control). Beberapa PLC dapat memberikan input ke CNC untuk
kepentingan pemrosesan lebih lanjut. CNC bila dibandingkan dengan PLC mempunyai
ketelitian yang lebih tinggi dan lebih mahal harganya. CNC biasanya dipakai
untuk proses finishing, membentuk benda kerja, moulding dan sebagainya.
Prinsip kerja sebuah PLC adalah menerima sinyal masukan proses yang dikendalikan
lalu melakukan serangkaian instruksi logika terhadap sinyal masukan tersebut
sesuai dengan program yang tersimpan dalam memori lalu menghasilkan sinyal
keluaran untuk mengendalikan aktuator atau peralatan lainnya.
![]() |
Gambar 2.1 Hubungan PLC
dengan CNC
2.2 Keuntungan dan Kerugian PLC [2][5]
Dalam industri-industri yang ada sekarang ini, kehadiran PLC sangat dibutuhkan
terutama untuk menggantikan sistem wiring atau pengkabelan yang sebelumnya
masih digunakan dalam mengendalikan suatu sistem. Dengan menggunakan PLC akan
diperoleh banyak keuntungan diantaranya adalah sebagai berikut:
Ø Fleksibel
Pada masa lalu, tiap perangkat elektronik
yang berbeda dikendalikan dengan pengendalinya masing-masing. Misal sepuluh
mesin membutuhkan sepuluh pengendali, tetapi kini hanya dengan satu PLC
kesepuluh mesin tersebut dapat dijalankan dengan programnya
masing-masing.
Ø Perubahan dan pengkoreksian kesalahan sistem
lebih mudah
Bila salah satu sistem akan diubah atau
dikoreksi maka pengubahannya hanya dilakukan pada program yang terdapat di
komputer, dalam waktu yang relatif singkat, setelah itu didownload ke PLC-nya.
Apabila tidak menggunakan PLC, misalnya relay maka perubahannya dilakukan
dengan cara mengubah pengkabelannya. Cara ini tentunya memakan waktu yang lama.
Ø Jumlah kontak yang banyak
Jumlah kontak yang dimiliki oleh PLC pada
masing-masing coil lebih banyak daripada kontak yang dimiliki oleh sebuah
relay.
Ø Harganya lebih murah
PLC mampu menyederhanakan banyak pengkabelan
dibandingkan dengan sebuah relay. Maka harga dari sebuah PLC lebih murah
dibandingkan dengan harga beberapa buah relay yang mampu melakukan pengkabelan
dengan jumlah yang sama dengan sebuah PLC. PLC mencakup relay, timers,
counters, sequencers, dan berbagai fungsi lainnya.
Ø Pilot running
PLC yang terprogram dapat dijalankan dan
dievaluasi terlebih dahulu di kantor atau laboratorium. Programnya dapat
ditulis, diuji, diobserbvasi dan dimodifikasi bila memang dibutuhkan dan hal
ini menghemat waktu bila dibandingkan dengan sistem relay konvensional yang
diuji dengan hasil terbaik di pabrik.
Ø Observasi visual
Selama program dijalankan, operasi pada PLC
dapat dilihat pada layar CRT. Kesalahan dari operasinya pun dapat diamati bila
terjadi.
Ø Kecepatan operasi
Kecepatan operasi PLC lebih cepat
dibandingkan dengan relay. Kecepatan PLC ditentukan dengan waktu scannya dalam
satuan millisecond.
Ø Metode Pemrograman Ladder atau Boolean
Pemrograman PLC dapat dinyatakan dengan
pemrograman ladder bagi teknisi, atau aljabar Boolean bagi programmer yang
bekerja di sistem kontrol digital atau Boolean.
Ø Sifatnya tahan uji
Solid state device lebih tahan uji
dibandingkan dengan relay dan timers mekanik atau elektrik. PLC merupakan solid
state device sehingga bersifat lebih tahan uji.
Ø Menyederhanakan komponen-komponen sistem
kontrol
Dalam PLC juga terdapat counter, relay dan
komponen-komponen lainnya, sehingga tidak membutuhkan komponen-komponen
tersebut sebagai tambahan. Penggunaan relay membutuhkan counter, timer ataupun
komponen-komponen lainnya sebagai peralatan tambahan.
Ø Dokumentasi
Printout dari PLC dapat langsung diperoleh
dan tidak perlu melihat blueprint circuit-nya.
Tidak seperti relay yang printout sirkuitnya tidak dapat diperoleh.
Ø Keamanan
Pengubahan pada PLC tidak dapat dilakukan
kecuali PLC tidak dikunci dan diprogram. Jadi tidak ada orang yang tidak
berkepentingan dapat mengubah program PLC selama PLC tersebut dikunci.
Ø Dapat melakukan pengubahan dengan pemrograman
ulang
Karena PLC dapat diprogram ulang secara
cepat, proses produksi yang bercampur dapat diselesaikan. Misal bagian B akan
dijalankan tetapi bagian A masih dalam proses, maka proses pada bagian B dapat
diprogram ulang dalam satuan detik.
Ø Penambahan rangkaian lebih cepat
Pengguna dapat menambah rangkaian pengendali
sewaktu-waktu dengan cepat, tanpa memerlukan tenaga dan biaya yang besar
seperti pada pengendali konvensional.
Selain keuntungan yang telah disebutkan di
atas maka ada kerugian yang dimiliki oleh PLC, yaitu:
Ø Teknologi yang masih baru
Pengubahan sistem kontrol lama yang
menggunakan ladder atau relay ke konsep komputer PLC merupakan hal yang sulit
bagi sebagian orang
Ø Buruk untuk aplikasi program yang tetap
Beberapa aplikasi merupakan aplikasi dengan
satu fungsi. Sedangkan PLC dapat mencakup beberapa fungsi sekaligus. Pada
aplikasi dengan satu fungsi jarang sekali dilakukan perubahan bahkan tidak sama
sekali, sehingga penggunaan PLC pada aplikasi dengan satu fungsi akan
memboroskan (biaya).
Ø Pertimbangan lingkungan
Dalam suatu pemrosesan, lingkungan mungkin
mengalami pemanasan yang tinggi, vibrasi yang kontak langsung dengan alat-alat
elektronik di dalam PLC dan hal ini bila terjadi terus menerus, mengganggu
kinerja PLC sehingga tidak berfungsi optimal.
Ø Operasi dengan rangkaian yang tetap
Jika rangkaian pada sebuah operasi tidak
diubah maka penggunaan PLC lebih mahal dibanding dengan peralatan kontrol
lainnya. PLC akan menjadi lebih efektif bila program pada proses tersebut di-upgrade secara periodik.
2.3 Rangkaian Start-Stop [5]
Banyak sistem mempunyai sebuah sistem Master
Control Relay untuk Safety
Shutdown pada operasi PLC. Ketika
ON, safety shutdown mengijinkan PLC untuk beroperasi. Ketika di-deenergize,
maka PLC tidak akan beroperasi. Tipe sistem master
shutdown seperti yang terlihat
pada gambar di halaman berikut:

Gambar 2.2 Skema Master
Control Safety Shutdown
Pada gambar di atas jika tombol Start di tekan (ON) maka coil MCR akan
ter-energize sehingga anak relay MCR akan ter-energize pula sehingga PLC akan
beroperasi. Walaupun tombol Start kembali ke posisinya semula (OFF), coil MCR
tetap ter-energize karena adanya anak relay MCR lain pararel dengan tombol
Start. Ketika tombol Stop ditekan (OFF), maka rangkaian menjadi terbuka yang
menyebabkan tidak ada lagi aliran arus ke coil MCR, sehingga coil MCR tidak
ter-energize lagi. Karena coil MCR tidak ter-energize lagi maka dua anak
relaynya akan OFF sehingga PLC akan OFF (tidak beroperasi).
Pada gambar di atas terdapat pula Emergency
Stop Pushbutton yang digunakan apabila terjadi sesuatu pada
sistem sehingga sistem harus dimatikan. Selain itu terdapat sebuah limit switch yang
berhubungan dengan pintu dimana sistem PLC diletakkan. Apabila pintu tersebut
dibuka maka limit switch OFF sehingga coil MCR tidak ter-energize yang
menyebabkan sistem PLC akan OFF, apabila pintu ditutup maka limit switch akan
ON sehingga sistem PLC akan ON pula. Sedangkan Suppressor digunakan untuk mengurangi atau
menghilangkan sinyal gangguan dari luar yang dapat membuat program sistem
PLC menjadi malfunction.
2.4 Bagian-Bagian PLC
Sistem PLC terdiri dari
lima bagian pokok, yaitu:
Ø Central
processing unit (CPU).
Bagian ini merupakan otak
atau jantung PLC, karena bagian ini merupakan bagian yang melakukan operasi /
pemrosesan program yang tersimpan dalam PLC. Disamping itu CPU juga melakukan
pengawasan atas semua operasional kerja PLC, transfer informasi melalui internal
bus antara PLC, memory dan unit I/O.
Bagian CPU ini antara
lain adalah :
q Power
Supply, power supply mengubah suplai
masukan listrik menjadi suplai listrik yang sesuai dengan CPU dan seluruh
komputer.
q Alterable
Memory, terdiri dari banyak bagian, intinya bagian ini berupa
chip yang isinya di letakkan pada chip RAM (Random Access Memory), tetapi
isinya dapat diubah dan dihapus oleh pengguna / pemrogram. Bila tidak ada
supplai listrik ke CPU maka isinya akan hilang, oleh sebab itu bagian ini
disebut bersifat volatile, tetapi ada juga
bagian yang tidak bersifat volatile.
q Fixed
Memory, berisi program yang sudah diset oleh pembuat PLC, dibuat
dalam bentuk chip khusus yang dinamakan ROM (Read Only Memory), dan
tidak dapat diubah atau dihapus selama operasi CPU, karena itu bagian ini
sering dinamakan memori non-volatile yang tidak akan terhapus
isinya walaupun tidak ada listrik yang masuk ke dalam CPU. Selain itu dapat
juga ditambahkan modul EEPROM atau Electrically
Erasable Programmable Read Only Memory yang
ditujukan untuk back up program utama RAM prosesor sehingga prosesor
dapat diprogram untuk meload program EEPROM ke RAM jika program di RAM hilang
atau rusak [6].
q Processor, adalah
bagian yang mengontrol supaya informasi tetap jalan dari bagian yang satu
ke bagian yang lain, bagian ini berisi rangkaian clock, sehingga
masing-masing transfer informasi ke tempat lain tepat sampai pada waktunya
q Battery
Backup, umumnya CPU memiliki bagian ini. Bagian ini berfungsi
menjaga agar tidak ada kehilangan program yang telah dimasukkan ke dalam RAM
PLC jika catu daya ke PLC tiba-tiba terputus.
Ø Programmer
/ monitor (PM).
Pemrograman dilakukan
melalui keyboard sehingga alat ini dinamakan Programmer. Dengan
adanya Monitor maka dapat dilihat apa yang diketik atau proses yang
sedang dijalankan oleh PLC. Bentuk PM ini ada yang besar seperti PC, ada juga
yang berukuran kecil yaitu hand-eld programmer dengan jendela tampilan yang
kecil, dan ada juga yang berbentuk laptop. PM dihubungkan dengan CPU melalui
kabel. Setelah CPU selesai diprogram maka PM tidak dipergunakan lagi untuk
operasi proses PLC, sehingga bagian ini hanya dibutuhkan satu buah untuk banyak
CPU.

Fiber optics cables
Or
Twisted pair of wires plus
ground
Or
Coaxial Cable
Multiple
wires
To
input
Multiple
wires
optional
To output
remote
connection up
to One
Mile
I/O
module
optional
connection
to
Connections
master
computer
to input
switches
contacts, etc
Connections
To Outputs-
Coils
Alarms,etc
Gambar 2.3 Layout Sistem PLC dan koneksinya
Ø Modul
input / output (I/O).
Input merupakan
bagian yang menerima sinyal elektrik dari sensor atau komponen lain dan sinyal
itu dialirkan ke PLC untuk diproses. Ada banyak jenis modul input yang
dapat dipilih dan jenisnya tergantung dari input yang
akan digunakan. Jika input adalah limit switches dan pushbutton dapat
dipilih kartu input DC. Modul input analog adalah kartu input khusus
yang menggunakan ADC (Analog to Digital Conversion)
dimana kartu ini digunakan untuk input yang berupa variable seperti temperatur,
kecepatan, tekanan dan posisi. Pada umumnya ada 8-32 input point setiap modul inputnya.
Setiap point akan ditandai sebagai alamat yang unik oleh prosesor.
Output adalah
bagian PLC yang menyalurkan sinyal elektrik hasil pemrosesan PLC ke peralatan
output. Besaran informasi / sinyal elektrik itu dinyatakan dengan tegangan
listrik antara 5 - 15 volt DC dengan informasi diluar sistem tegangan yang
bervariasi antara 24 - 240 volt DC mapun AC. Kartu output biasanya
mempunyai 6-32 output point dalam sebuah single module. Kartu output analog adalah tipe khusus dari modul output yang
menggunakan DAC (Digital to Analog Conversion). Modul output analog
dapat mengambil nilai dalam 12 bit dan mengubahnya ke dalam signal analog. Biasanya
signal ini 0-10 volts DC atau 4-20 mA. Signal Analog biasanya digunakan pada
peralatan seperti motor yang mengoperasikan katup dan pneumatic
position control devices.
Bila dibutuhkan, suatu
sistem elektronik dapat ditambahkan untuk menghubungkan modul ini ke tempat
yang jauh. Proses operasi sebenarnya di bawah kendali PLC mungkin saja jaraknya
jauh, dapat saja ribuan meter.
Ø Printer.
Alat ini memungkinkan
program pada CPU dapat di printout atau dicetak. Informasi yang mungkin dicetak
adalah diagram ladder, status register, status dan daftar dari kondisi-kondisi
yang sedang dijalankan, timing diagram dari kontak, timing diagram dari
register, dan lain-lain.
Ø The Program Recorder /
Player.
Alat ini digunakan
untuk menyimpan program dalam CPU. Pada PLC yang lama digunakan tape, sistem floopy
disk. Sekarang ini PLC semakin berkembang
dengan adanya hard disk yang digunakan untuk pemrograman dan perekaman. Program
yang telah direkam ini nantinya akan direkam kembali ke dalam CPU apabila
program aslinya hilang atau mengalami kesalahan.
Untuk operasi yang besar,
kemungkinan lain adalah menghubungkan CPU dengan komputer utama (master
computer) yang biasanya digunakan pada pabrik besar atau proses yang
mengkoodinasi banyak Sistem PLC .
Dalam merancang suatu sistem kendali dibutuhkan pendekatan-pendekatan
sistematis dengan prosedure sebagai berikut :
1.
Rancangan Sistem Kendali
Dalam tahapan ini si
perancang harus menentukan terlebih dahulu sistem apa yang akan dikendalikan
dan proses bagaimana yang akan ditempuh. Sistem yang dikendalikan dapat berupa
peralatan mesin ataupun proses yang terintegrasi yang sering secara umum
disebut dengan controlled system.
2.
Penentuan I/O
Pada tahap ini semua piranti masukan dan
keluaran eksternal yang akan dihubungkan PLC harus ditentukan. Piranti masukan
dapat berupa saklar, sensor, valve dan lain-lain sedangkan piranti keluaran
dapat berupa solenoid katup elektromagnetik dan lain-lain.
3.
Perancangan Program (Program Design)
Setelah ditentukan input dan output maka
dilanjutkan dengan proses merancang program dalam bentuk ladder diagram
dengan mengikuti aturan dan urutan operasi sistem kendali.
4.
Pemrograman (Programming)
5.
Menjalankan Sistem (Run The System)
Pada tahapan ini perlu dideteksi adanya
kesalahan-kesalahan satu persatu (debug), dan menguji secara cermat sampai kita
memastikan bahwa sistem aman untuk dijalankan.
Langganan:
Postingan (Atom)